Project Overview
A textile manufacturer partnered with Octans Digital to address inefficiencies in production processes caused by manual data entry, Excel spreadsheets, and a lack of integration between their Manufacturing Execution System (MES) and ERP. This led to delays in decision-making, data inconsistencies, and poor communication, affecting overall operational responsiveness.
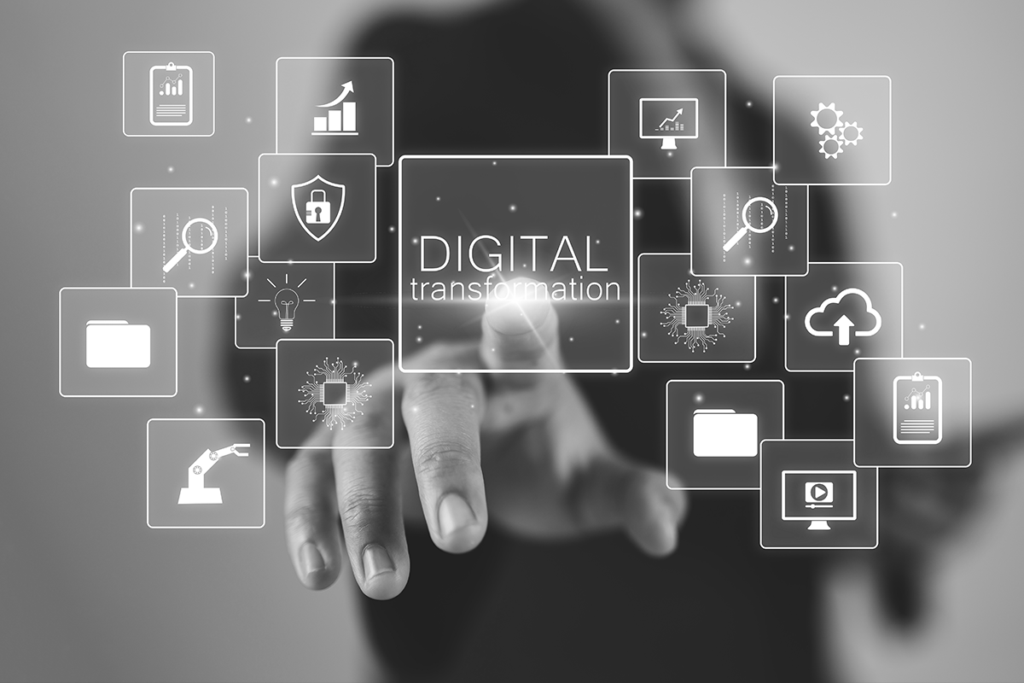
Client Challenges
- Inefficient Communication: Gaps in communication between the shop floor and management slowed problem resolution.
- Lack of Real-Time Visibility: Delayed decision-making due to the absence of real-time production data.
- Human Errors and Data Inconsistencies: Manual data entry and reliance on multiple spreadsheets led to frequent errors and data hygiene issues.
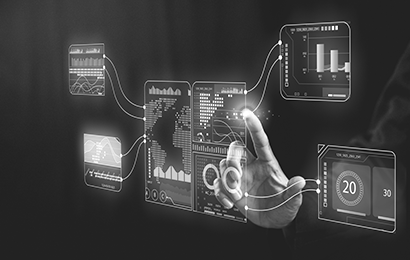
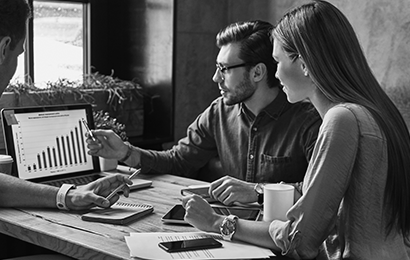
Solutions Implemented
- MES Integration with ERP: Seamless integration of MES with ERP enabled real-time data flow, improving synchronization between production and management systems.
- Enhanced Decision-Making and Data Integrity: Real-time production data and automated data entry led to quicker decision-making and improved data consistency and accuracy.
- Improved Communication and Sustainability: Enhanced communication channels between the shop floor and management, along with a shift to paperless operations, supported operational efficiency and sustainability goals.
Impact Delivered
- Enhanced Real-Time Visibility: MES integration provided real-time insights, enabling quicker responses to issues and more agile operations.
- Improved Data Integrity and Accountability: Automation and integration reduced errors, ensuring consistent data and fostering transparency and accountability within teams.
- Sustainable and Paperless Operations: The digital workflow transition contributed to sustainability by reducing paper usage and waste, supporting the company’s eco-friendly initiatives.
Why This Project Stands Out
- Operational Efficiency & Data Integrity: MES-ERP integration streamlined processes and improved data accuracy.
- Enhanced Decision-Making: Real-time insights enabled better management and strategic planning.
- Sustainability & Growth: The project supported eco-friendly initiatives and positioned the company for long-term success.
Conclusion
The Fog Light project has transformed the textile manufacturer’s production processes, enhancing real-time decision-making and eliminating inefficiencies. By integrating MES with ERP, the company improved data integrity, streamlined operations, and strengthened communication between the shop floor and management. This digital transformation boosts efficiency, supports sustainability, and positions the manufacturer for long-term success in a competitive industry.
Snapshot
Client
A textile manufacturer.
Challenge
Lack of real-time production visibility, human errors due to manual data entry, and inefficient communication between the shop floor and management.
Solution
Integration of MES with ERP to enable real-time data flow, automate data entry, improve communication, and transition to paperless operations.
Outcome
Enhanced real-time visibility, improved data integrity, faster decision-making, and sustainable, paperless operations that supported eco-friendly goals and long-term growth.